Введение
В статье “Молибден. Свойства, применение, производство, продукция” подробно рассматривается тугоплавкий металл молибден. Описаны свойства молибдена, указаны области его применения. Также перечислены различные марки молибдена с указанием их особенностей.Статья освещает процесс производства молибдена от стадии обогащения руды до стадии получения заготовок в виде штабиков и слитков. Отмечаются характерные особенности каждой стадии.
Особое внимание в статье уделяется продукции (проволока, прутки, листы, полосы, порошок и др.). Описаны процессы изготовления той или иной продукции из молибдена, ее характерные особенности и области применения.
Статья содержит ссылки на стандарты, такие как ГОСТ и ТУ, на другие статьи, описывающие смежные темы.
Глава 1. Молибден. Свойства и области применения молибдена
Молибден (обозначается Mo) - химический элемент VI группы 5-го периода таблицы Д.И. Менделеева, имеет номер 42; переходный металл светло-серого цвета. Он относится к разряду тугоплавких металлов, имеет температуру плавления tпл = 2620 °С. Рассматривая различные применения молибдена в качестве металла, наиболее важными свойствами следует считать плотность, температуру плавления, электрическое сопротивление, коэффициент линейного расширения.§1. Свойства молибдена
Основные физические и механические свойства молибдена представлены в таблице. Стоит также заметить, что электропроводность молибдена выше по сравнению с электропроводностью железа и ниже, чем аналогичное свойство меди. По механической прочности молибден немного уступает вольфраму, но, в тоже время, легче поддается обработке давлением.Свойство | Значение |
---|---|
Физические свойства | |
Атомный номер | 42 |
Атомная масса, а.е.м. (г/моль) | 95,94 |
Атомный диаметр, нм | 0,273 |
Плотность, г/см3 | 10,2 |
Температура плавления, °С | 2620 |
Температура кипения, °С | 4830 |
Удельная теплоемкость, Дж/(г•К) | 0,248 |
Теплопроводность, Вт/(м•K) | 138 |
Электрическое сопротивление, мкОм•см | 5,7 |
Коэффициент линейного термического расширения, 10-6 м/мК | 4,9 |
Механические свойства | |
Модуль Юнга, ГПа | 329,3 |
Модуль сдвига, ГПа | 122,0 |
Коэффициент Пуассона | 0,30 |
Временное сопротивление σB, МПа | 800-900 |
Относительное удлинение δ, % | 0-15 |
§2. Марки молибдена
Марка молибдена | Характеристика марки |
---|---|
МЧ | Молибден чистый без присадок |
МЧВП | Молибден чистый без присадок, полученный с помощью вакуумной плавки |
МРН | Молибден без присадок. Молибден разного назначения. Температура рекристализации молибдена этой марки может быть несколько выше, чем у молибдена марки МЧ за счет большего содержания примесей |
МК | Молибден с кремнещелочной присадкой. Характеризуется значительно более высокой температурой рекристализации, по сравнению с молибденом марки МЧ и более высокой прочностью при изгибе в отожженном состоянии |
МР | Сплавы молибдена и рения |
ЦМ | Молибден с присадкой циркония и/или титана |
МВ | Сплавы молибдена и вольфрама |
Жаропрочные материалы на основе молибдена можно разделить на четыре группы:
- практически чистый молибден;
- низколегированные малоуглеродистые сплавы;
- низколегированные высокоуглеродистые сплавы;
- высоколегированные сплавы.
Во вторую группу входят такие сплавы молибдена, как ЦМ5, ЦМ6, ЦМ-2А, ВМ-1, ТСМ4 с типичным содержанием углерода (по массе) 0,004-0,05% С, а также сплавы ЦМ10 и ТСМ-7 с пониженным содержанием углерода. Сплавы ЦМ5 и ЦМ6 относятся к системе молибден-цирконий (Mo-Zr), а сплавы ЦМ-2А, ВМ-1 легированы одновременно небольшими добавками титана и циркония. Сплав ТСМ4, помимо циркония, содержит небольшие концентрации никеля и углерода, это сплав системы молибден-цирконий-никель-углерод (Mo-Zr-Ni-C). Среди сплавов второй группы наиболее широко распространен малолегированный сплав ЦМ-2А, отличающийся достаточной технологичностью и более высокой жаропрочностью по сравнению с чистым молибденом. Сплав ЦМ-2А наименее склонен к хладноломкости после деформации. Рекристаллизация повышает его склонность к хрупкости. Сплав ВМ-1 по составу и свойствам близок к сплаву ЦМ-2А. Сплав ЦМ5 более жаропрочен, чем ЦМ-2А. Сплав ЦМ6 с меньшим содержанием циркония и углерода уступает сплаву ЦМ5 по жаропрочности, но является более технологичным, менее склонен к хладноломкости в рекристаллизованном состоянии, хорошо сваривается.
В третью группу (низколегированные высокоуглеродистые сплавы) входит ВМ-3 с повышенным содержанием углерода, доходящим (по массе) до 0,25-0,50%. Чтобы связать весь углерод в карбиды, этот сплав легирован большим количеством титана и циркония; дополнительное упрочнение обеспечивает ниобий. Карбиды титана (TiC) и циркония (ZrC) улучшают жаропрочность сплава. В то же время карбид молибдена (Mo2C) оказывает негативное влияние на технологические свойства сплавов. Его присутствие снижает пластичность как при комнатной, так и при высокой температуре. Для исключения образования Mo2C титан, цирконий и углерод вводят в сплавы в определенных пропорциях.
К четвертой группе (высоколегированные сплавы) относятся ЦМВ30, ЦМВ50 и МР47ВП. Для сплавов ЦМВ30 и ЦМВ50 характерна высокая жаропрочность, обусловленная их легированием большими количествами вольфрама, а сплав МР47ВП системы молибден-рений (Mo-Re) отличается высокими прочностными свойствами при умеренных температурах и большой технологичностью. Жаропрочность последнего сплава может быть существенно повышена введением карбидов ZrC и ТiС.
§3. Области применения молибдена
Тугоплавкий металл молибден нашел широкое применение в современной промышленности как в качестве легирующей добавки к различным сплавам, так и в качестве конструкционного материала.Основные направления применения молибдена
1. Легирующий элемент в различных сталях и сплавах цветных металлов
В качестве легирующей добавки молибден активно используется в черной металлургии при производстве сталей и чугунов. В состав конструкционных сталей входит до 0,5 % данного тугоплавкого металла. Благодаря молибдену значительно улучшается структура конструкционной стали. Она становится более однородной и мелкозернистой. Добавление молибдена позволяет улучшить механические свойства сталей и сплавов, а именно: предел упругости, сопротивление износу и удару. Одно из ценных свойств молибдена – его способность устранять отпускную хрупкость аустенитной стали.
Молибден активно применяется при производстве различных инструментальных сталей. Стали, из которых изготавливают штампы, обычно содержат 1-1,5 % данного тугоплавкого металла, быстрорежущие стали – 5-8,5 %. Молибден повышает красностойкость инструментальных сталей, их твердость, прочность, сопротивление образованию закалочных трещин, износу.
Хромистые и хромоникелевые стали также имеют в своем составе молибден. Он снижает хрупкость и повышает жаропрочность данных сталей в условиях длительной работы. Введение 2-4 % молибдена в нержавеющие хромоникелевые стали улучшает их коррозионную стойкость.
Тугоплавкий металл молибден также включают и в состав чугунов. Введение в чугун 0,2-0,5 % молибдена повышает вязкость, сопротивление износу и улучшает свойства при высоких температурах, а также уменьшает склонность к росту зерен.
2. Антикоррозионные и жаропрочные сплавы
Очень часто молибден входит в состав жаропрочных и кислотостойких сплавов. Металлы кобальт и никель, как правило, являются основой жаропрочных сплавов (50-60 %), также такие сплавы содержат хром (20-28 %) и молибден (3-10 %). В качестве примера можно привести жаропрочный сплав, который используется для изготовления лопаток и дисков роторов газовых турбин: Ni – 37 %, Co – 20 %, Cr – 18 %, Fe – 17 %, Mo – 3 %, Ti – 2,8 %
Кислотостойкие сплавы, содержащие 17-28 % молибдена, а также хром, вольфрам и железо, устойчивы к воздействию всех минеральных кислот (например, серная кислота, соляная кислота и другие), кроме плавиковой.
3. Конструкционный материал в аэрокосмической и атомной технике
Благодаря своим свойствам молибден используется в качестве конструкционного материала в аэрокосмической и атомной технике. Конструкционные металлы и сплавы, применяемые в аэрокосмической отрасли, должны отличаться хорошей жаропрочностью и окалиностойкостью . Данными свойствами обладают тугоплавкие металлы вольфрам, молибден, ниобий и другие, однако, ниобий и молибден имеют большую удельную прочность при температуре до 1370 °С по сравнению с вольфрамом, поэтому более предпочтительны в качестве конструкционных материалов, работающих при указанной и более низких температурах.
Молибден используется для изготовления обшивки и элементов каркаса сверхзвуковых самолетов и ракет, а также теплообменников, оболочек возвращающихся на землю ракет и капсул, тепловых экранов, передних кромок ракет, носовых конусов ракет, обшивки кромок крыльев сверхзвуковых самолетов.
Молибден с присадками ниобия, ванадия, титана и других металлов, которые повышают жаропрочность, применяется для изготовления ответственных деталей ракетных двигателей и газовых турбин: сопловые и рабочие лопатки газовых турбин, выхлопные сопла и камеры сгорания прямоточных реактивных двигателей.
Металл молибден является тугоплавким и достаточно хорошо устойчив к воздействию жидких металлических теплоносителей типа лития и свинцововисмутового сплава. Указанные свойства молибдена позволяют использовать его в качестве конструкционного материала в энергетических атомных реакторах при температуре до 800 °С. Из тугоплавкого металла молибден изготовляют контейнеры, оболочки, трубы и другие элементы активной зоны реактора.
4. Материал для изготовления оборудования для обработки металлов давлением
Жаропрочность молибдена, его тугоплавкость, высокая теплопроводность и низкий коэффициент расширения позволяют использовать данный метал для изготовления элементов оборудования, предназначенного для горячей обработки металлов давлением. Так из молибдена производят оправки прошивных станов, матрицы, пресс-штемпели. Стоит заметить, что по данным экспериментов прошивные пуансоны для прошивки заготовок из нержавеющей стали, изготовленные из сплава молибдена с 0,5% титана, прошивают до момента выхода из строя в 100 раз больше заготовок по сравнению с пуансонами из других материалов. Также из тугоплавкого металла молибден производят пресс-формы и стержни машин для литья под давлением сплавов меди, цинка и алюминия.
5. Материал для изготовления нагревателей высокотемпературных печей
Проволоку, ленту и прутки из молибдена применяют в качестве нагревателей высокотемпературных электрических печей. Температура в таких печах может достигать 1700 - 2000 °С. Стоит заметить, что молибденовые нагреватели должны работать только в защитной атмосфере (обычно, водород, аргон) или в вакууме.
Молибденовые прутки применяют также в качестве электродов в печах для плавки стекла. Как правило, для данных целей используют прутки диаметром от 25 до 150 мм и длиной до 1,8 м. Также встречаются плавильные печи с электродами в виде молибденовых пластин. Стоит заметить, что молибден практически не вступает в реакцию с расплавленным стеклом. Это позволяет использовать данный металл для изготовления деталей стеклоплавильных печей.
6. Материал для производства электроламп и электровакуумной техники
Такие свойства, как жаропрочность, высокая электропроводность, высокая температура плавления, позволяют применять молибден в производстве электроламп и электровакуумных приборов. Молибденовая проволока применяется для изготовления крючков, которые поддерживают вольфрамовую нить в лампе накала. Также молибден используют в качестве керна для навивки вольфрамовой проволоки.
Молибденовые прутки служат для ввода тока в различные электровакуумные приборы и колбы мощных источников света. Листы из молибдена применяются для производства анодов генераторных ламп. Также из данного метала изготовляют сетки приемно-усилительных ламп, вспомогательные электроды генераторных ламп, катоды газоразрядных трубок.
Молибден также нашел применение и в рентгеновской технике. Например, из него производят фокусирующие электроды, вводы катодов.
Глава 2. Производство молибдена
§1. Процесс получения тугоплавкого металла молибден
Молибден принято относить к широкой группе редких металлов . Помимо данного металла в эту группу входят вольфрам, ванадий и другие. Для редких металлов характерны сравнительно небольшие масштабы производства и потребления, а также малая распространенность в земной коре. Например, как правило, содержание молибдена в рудах составляет сотые и тысячные доли процента. Ни один редкий металл не получают непосредственным восстановлением из сырья. Сначала сырье перерабатывается на химические соединения. Кроме того, все редкометаллические руды подвергаются дополнительному обогащению перед переработкой.В процессе получения редкого металла можно выделить три основных стадии:
- Разложение рудного материала - отделение извлекаемого металла от основной массы перерабатываемого сырья и концентрирование его в растворе или осадке.
- Получение чистых химических соединений - выделение и очистка химического соединения.
- Выделение металла из полученного соединения - получение чистых редких металлов.
Процесс получения молибдена состоит из нескольких стадий.
- Обогащение молибденовой руды. Оно производится с помощью флотации. В результате обогащения получают молибденитовые концентраты, содержащие 90 - 95 % MoS2. Промышленность выпускает концентраты трех марок: КМ1 (содержит не менее 50% молибдена), КМ2 (содержит не менее 48% молибдена) и КМ3 (содержит не менее 47% молибдена). В молибденитовых концентратах контролируется содержание примесей - фосфора, мышьяка, олова, меди и кремнезема. Если обогащению подвергаются полиметаллические молибденовые руды, то, как правило, содержание молибдена в концентратах составляет 15-20%.
- Получение трехокиси (ангидрида) молибдена MoO3, который служит исходным сырьем для производства металлического молибдена. Сначала получают огарок (оксид молибдена MoO3, содержащий большое количество примесей) из молибденитового концентрата (MoS2) путем окислительного обжига последнего. Далее из огарка получают молибденовый ангидрид (чистый MoO3). Для этого могут применяться такие процессы, как возгонка или гидрометаллургическая (химическая) переработка огарка. В результате получают чистую трехокись молибдена с содержанием последнего не менее 99,975%
- Получение молибденового порошка. Исходным сырьем для получения чистого металла служит ангидрид молибдена MoO3. Для производства чистого молибденового порошка проводят процесс восстановления ангидрида водородом. Восстановление осуществляется в три стадии: восстановление MoO3 до MoO2 при температуре 450-600 °С; восстановление MoO2 при температуре 950 °С до металла, содержащего 0,5-1,5% кислорода; уменьшение содержания кислорода в металле ниже 0,25-0,3% путем восстановления при температуре 1000-1100 °С. В результате получают чистый молибденовый порошок, имеющий среднюю крупность зерен около 0,5-2 мкм.
- Получение компактного молибдена. Компактный молибден, как правило, в виде штабиков или слитков является заготовкой для производства полуфабрикатов, таких, как проволока, пруток, лента и так далее.
§2. Получение компактного молибдена
Существуют два способа получения компактного молибдена. Первый заключается в применении методов порошковой металлургии. Второй - с помощью плавки в печах различного принципа действия.Методы порошковой металлургии
Данный способ получения ковкого молибдена является наиболее распространенным, так как позволяет более равномерно распределять присадки, которые улучшают физико-механические свойства молибдена. В качестве присадок могут использоваться титан (Ti), цирконий (Zr), ванадий (V) и другие металлы.
Процесс получения компактного молибдена методом порошковой металлургии состоит из нескольких стадий:
- прессование штабиков из металлического порошка - формовка;
- низкотемпературное (предварительное) спекание заготовок;
- спекание (сварка) заготовок;
- обработка заготовок с целью получения полуфабрикатов - молибденовой проволоки, прутков и других полуфабрикатов; обычно заготовки обрабатывают под давлением (ковкой) или подвергают механической обработке резанием (например, шлифование, полирование).
Предварительное спекание штабиков обычно проводят в муфельных или трубчатых печах при температуре 1110-1200 °С. Спекание (сварку) осуществляют при температуре 2200-2400 °С в специальных аппаратах для высокотемпературного спекания. Если заготовки крупногабаритные, то для их спекания предпочтительнее использовать печь с косвенным нагревом. Примером подобной печи является вакуумная печь непрерывного действия для высокотемпературного спекания штабиков косвенным нагревом, где в качестве нагревателей используются графитовые стержни. Стоит заметить, что предварительное спекание штабиков осуществляется в среде водорода, что способствует упрочнению заготовки и повышению электропроводности.
Плавка
Плавка используется для получения компактного молибдена в виде крупногабаритных заготовок (от 200 до 2000 кг), предназначенных для проката, вытяжки труб, производства изделий методом литья. Осуществляется плавка в электрических дуговых печах с расходуемым электродом и/или электронно-лучевая плавка . В результате плавки получаются молибденовые слитки .
При дуговой плавке в качестве электродов служат пакеты спеченных молибденовых прутков, которые, в свою очередь, получают путем сваривания (спекания) штабиков. Подобные прутки, как правило, имеют длину 1-2,5 м и объединяются в пакеты по 4-16 прутков, а в некоторых случаях и больше.
После дуговой плавки молибденовые слитки содержат следующие примеси (приблизительно), %: O2 – 1-3 ∙ 10-4, H2 – 1-2 ∙ 10-5, N2 – 10-3-10-4. В результате электронно-лучевой плавки удается избавиться от большого числа примесей, среди которых кислород, азот, углерод, железо, медь, никель, марганец, кобальт. Стоит заметить, что при получении молибденовых слитков любым из приведенных способов для глубокой очистки молибдена от кислорода (содержание в металле < 0,0001 %) необходимо вводить раскислитель . В качестве раскислителя обычно выступают такие элементы, как титан, цирконий или углерод.
Глава 3. Продукция из молибдена. Прутки, проволока, листы (полосы), порошок
Промышленность выпускает большое количество продукции из тугоплавкого металла молибден. В данном контексте стоит выделить продукцию круглого сечения - молибденовые прутки и проволоку, плоский прокат – полосы, листы и ленты из молибдена, а также порошки.Заготовками для производства перечисленной выше продукции могут служить спеченные молибденовые штабики (изготовлены методом порошковой металлургии) или слитки (изготовлены методом литья). Большинство продукции из металла молибден получают путем обработки заготовок давлением. В зависимости от типа и размера заготовок технологические процессы производства продукции могут значительно отличаться.
§1. Молибденовые прутки
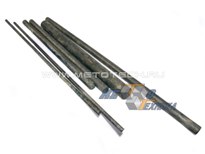
Молибденовые прутки – один из самых распространенных видов продукции из тугоплавкого металла молибден. Помимо самостоятельного назначения прутки из молибдена также могут служить заготовками для изготовления проволоки.
Исходными материалами для производства прутков являются спеченные молибденовые штабики квадратного сечения со стороной 40 мм и меньше, а также слитки плавленого молибдена различных размеров.
В процессе получения молибденовых прутков из штабиков последние подвергаются ротационной ковке. Ковка молибденовых прутков осуществляется в несколько этапов. На каждом этапе получают прутки определенных диаметров, при этом условия ковки специальным образом изменяются в зависимости от диаметра поступающей заготовки.
Устройство ротационной ковачной машины
1 - станина, 2 - вал, 3 - ролики, 4 - стальная обойма, 5 - ковочные плашки, 6 - спеченный штабик
На первом этапе штабики нагревают до тепературы 1350-1400 °С. Непосредственно ковку осуществляют при температуре около 1300 °С. В результате термической обработки плотность пористых штабиков увеличивается, а поры на границах зерен внутри кристаллов исчезают. В итоге прочность материала на растяжение резко повышается и в несколько раз превосходит прочность спеченного штабика. Как правило, для нагрева используются печи сопротивления с нагревателями из молибдена и водородной атмосферой. Для подогрева больших штабиков иногда применяют муфельные печи, в которые в зависимости от размеров муфеля можно помещать одновременно несколько штабиков. Печи размещаются рядом с ковочной машиной, чтобы избежать чрезмерного охлаждения штабиков во время их извлечения из печи и введения в рабочий канал машины. Подача заготовок в ковочную машину осуществляется вручную. На данном этапе получают прутки, диаметр которых составляет 20-25 мм. На следующих этапах температуру ковки постепенно уменьшают с уменьшением диаметра прутков. Ковку прутков, имеющих диаметр 2,5-3 мм, осуществляют при температуре 950-1000 °С.
Когда длина прутков значительно возрастает, переходят на непрерывную ковку. Данный переход осуществляют при диаметре прутка 3 мм, если исходными заготовками были штабики сечением 10х10 или 12х12 мм. Подача прутков в ковочную машину осуществляется механически, а для подогрева используется газовая печь. При непрерывной ковке прутки покрывают смазкой – аквадагом или гидроколлагом (водные коллоидные суспензии графита). Смазка предохраняет пруток от окисления и уменьшает износ матриц ковочной машины.
К недостаткам ротационной ковки можно отнести трудоемкость процесса и неровность поверхности получаемых прутков. При нагреве заготовок возникают значительные потери молибдена вследствие его окисления. Для снижения потерь и улучшения пластических свойств молибдена разработаны процессы ковки в атмосфере инертного газа.
Помимо спеченных штабиков заготовками для производства молибденовых прутков могут служить слитки. Слитки плавленого молибдена имеют грубую крупнозернистую структуру и значительно труднее поддаются обработке давлением, чем спеченные заготовки. Поэтому горячую ковку можно применять только для слитков диаметром до 100 мм. Ковка осуществляется при температуре 1400-1450 °С. Заготовки диаметром 150 мм и больше обрабатывают методом прессования. Ковка таких заготовок может привести к образованию трещин.
Перед прессованием слиток нагревают до температуры 760 °С, покрывают специальной эмалью, на которую затем накатывают тонкоизмельченное стекло. Стекло в данном случае выступает в качестве смазки. Затем заготовку нагревают до 1260 °С и еще раз покрывают стеклом. Далее осуществляется прессование. После прессования слитки подвергают горячей ковке при температуре 1425 °С. У полученного в результате ковки прутка обрезают концы. Затем пруток обтачивают на глубину до 25 мм с целью удаления стекла и слоя окалины. В дальнейшем прутки могут подвергаться ковке для получения необходимого размера.
Стоит заметить, что изделия из спеченных и плавленых заготовок молибдена не отличаются по свойствам.
Применение
Одним из направлений применения продукции из молибдена является изготовление нагревателей высокотемпературных электрических печей (см. Глава 1 §3). Молибденовые прутки могут использоваться в качестве таких нагревателей. Как правило, нагреватели из молибденовых прутков являются свободноизлучающими, то есть тепло передается от нагревателя непосредственно нагреваемому изделию, за счет чего достигается более эффективное использование мощности печи. Крепление таких нагревательных элементов должно быть очень надежным, чтобы исключить их провисание. Нагреватели из молибденовых прутков обладают высокой прочностью. Они используются в высокотемпературных электрических печах, обладающих большой мощностью.
Молибденовые прутки применяются для изготовления вводов электровакуумных приборов . Широкое распространение в данной области прутки из молибдена получили благодаря тому, что данный металл имеет достаточно высокую электропроводность и малый коэффициент термического расширения, отлично согласующийся с коэффициентом термического расширения тугоплавкого стекла, из которого сделаны корпусы электровакуумных приборов. Прутки из молибдена применяют для изготовления вводов, рассчитанных на большую силу тока, например, для вводов стеклянных вентилей.
Одной из наиболее важных областей применения молибденовых прутков является производство проволоки, где молибденовые прутки выступают в качестве заготовок (см. Глава 3 §2).
Стандарты
- ГОСТ 17432-72 «Материалы порошковые. Прутки и поковки из сплава марки М-МП. Технические условия».
- ТУ 11-77 (Яе0.021.057 ТУ) «Прутки молибденовые».
- ТУ 48-19-203-85 «Прутки из молибдена металлокерамического и вакуумной плавки, неотожженые. Технические условия».
- ТУ 48-19-247-87 «Прутки молибденовые диаметром от 16 до 125 мм. Технические условия».
- ТУ 48-19-273-91 «Прутки, поковки и листы из молибденового сплава марки ЦМ-2А. Технические условия».
§2. Молибденовая проволока
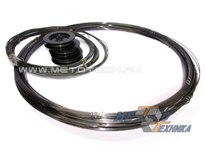
Молибденовая проволока - один из самых распространенных видов продукции из данного тугоплавкого металла.
Исходными материалами для производства проволоки из молибдена являются прутки. Диаметр таких прутков обычно составляет менее 3 мм. При таком диаметре молибденовые прутки обладают достаточной пластичностью, чтобы их можно было наматывать на барабан или катушку для дальнейшего изготовления проволоки методом протяжки.
Принципиальная схема установки для протяжки молибденовой проволоки представлена на рисунке.
Устройство установки для протяжки молибденовой проволоки
1 – ведущий барабан, 2 – фильера, 3 – газовая печь, 4 – смазочная коробка, 5 – спускной барабан
Данный способ позволяет получить проволоку, диаметр которой составляет до 0,012-0,010 мм. Для изготовления более тонкой проволоки применяют методы химического или электролитического травления. Исходным материалом для указанных способов является проволока большего диаметра, чем тот, который требуется получить.
Протяжку осуществляют в несколько этапов. На каждом этапе получают молибденовую проволоку определенных диаметров, при этом условия протяжки несколько изменяются в зависимости от диаметра, который требуется получить. В общем случае с уменьшением диаметра проволоки уменьшается температура и увеличивается скорость протяжки, уменьшение диаметра за один переход составляет, как правило, 10-20%.
Можно выделить 4 основные стадии протяжки:
- грубое волочение – изготовление проволоки диаметром до 0,9 мм, температура подогрева - 700 °С;
- изготовление проволоки диаметром от 0,9 до 0,2 мм, температура подогрева – 600-500 °С;
- среднее волочение - изготовление проволоки диаметром от 0,2 до 0,06 мм, температура подогрева – 500-300 °С;
- тонкое волочение – изготовление проволоки диаметром менее 0,06 мм, температура подогрева – 500-300 °С.
Процесс протяжки проволоки происходит следующим образом. Проволоку или пруток, который является заготовкой, наматывают на спускной барабан/катушку. Диаметр барабана/катушки зависит от диаметра заготовки. Затем заготовка проходит через сосуд, содержащий смазку. В качестве смазки, обычно, используются составы, содержащие большое количество коллоидного графита. Для проволоки больших диаметров в качестве смазки, как правило, применяют гидроколлаг, для проволоки диаметром 0,06 мм и менее – аквадаг. Смазка предотвращает окисление проволоки во время предварительного подогрева, а также уменьшает износ фильер. После сосуда со смазкой проволока попадает в печь предварительного подогрева. Подогрев необходим, чтобы улучшить пластичность заготовки. Наиболее распространенными способами подогрева являются подогрев в газовой печи и подогрев с помощью прямого пропускания тока через заготовку. В некоторых случаях применяют косвенный нагрев в электрической печи сопротивления с нихромовыми нагревателями. При нагреве в газовой печи отрезок проволоки прогревается равномерно, в отличие от нагрева с помощью прямого пропускания тока через проволоку, при котором один из концов отрезка нагревается сильнее (возникает градиент температуры). Стоит заметить, что помимо проволоки также осуществляется нагрев фильер . Нагрев фильер является нежелательным фактором и может привести к ухудшению качества производимой продукции. Далее проволоку протягивают через фильеры, где она подвергается деформации. Как правило, при диаметрах проволоки 0,3 мм и более применяют твердосплавные фильеры (обычно, карбид вольфрама + кобальт), при меньших диаметрах – алмазные. На завершающем этапе полученная проволока заданного диаметра наматывается на ведущий барабан/катушку, диаметр которого зависит от диаметра проволоки.
После волочения поверхность молибденовой проволоки очищают. Для очистки проволоку подвергают отжигу в атмосфере водорода при температуре 1300-1400 °С. Также для очистки поверхности могут применяться электролитическое травление (как правило, используется для очистки толстой проволоки), травление в расплаве азотистокислого натрия, отжиг в азоте.
При протяжке проволоки возможно возникновение дефектов. Среди наиболее часто встречающихся дефектов можно выделить растрескивание и расслоение проволоки (как правило, на стадии грубого волочения) или обрыв (при протяжке тонкой проволоки). Для предотвращения описанных дефектов следует использовать не загрязненный примесями исходный материал, четко соблюдать правильные режимы ковки штабиков и протяжки проволоки.
Применение
Молибденовая проволока нашла применение во многих отраслях промышленности. Одной из областей применения проволоки из молибдена является производство термопар для измерения высоких температур. Для этих целей обычно изготовляют термопары вольфрам-молибден и вольфрам-вольфрам/молибден . Сплав вольфрам/молибден содержит 25% молибдена. Для производства термопар используются материалы высокой чистоты. Спай на конце термопары получают с помощью дуговой сварки вольфрамовым электродом. Термопары вольфрам-молибден, вольфрам-вольфрам/молибден, как правило, имеют защитный чехол. В качестве материала защитных чехлов может использоваться окись циркония, которая не вступает во взаимодействие с материалами термопары.
Указанные термопары позволяют выполнять измерения температур, превышающих 2000 °С. Например, термопара вольфрам-вольфрам/молибден применялась в экспериментах по определению точки плавления молибдена, термопара вольфрам-молибден – точки плавления хрома.
Стоит заметить, что с изменением температуры термоэлектродвижущая сила (термо-ЭДС) изменяется сравнительно мало. Поэтому для точного измерения термо-ЭДС, на основе которого определяется температура, требуется использовать высокочувствительные приборы.
Молибденовая проволока используется при производстве ламп накаливания. Из нее изготовляют крючки и петли, поддерживающие вольфрамовую спираль, а также керны для навивки вольфрамовой спирали. Проволока из молибдена, применяемая для изготовления поддерживающих крючков и петель, не должна содержать железа, которое может привести к быстрому почернению оболочки лампы. Обычно используют блестящую неотожженную или полуотожженную проволоку диаметра от 0,02 до 1,1 мм, относительное удлинение которой составляет 5-15%. Применение молибдена в качестве материала для изготовления крючков и петель, поддерживающих вольфрамовую спираль, обусловлено его значительной прочностью при высоких температурах, а также сохранением данным металлом пластичности и прочности после рекристаллизации.
Керны для навивки спирали из вольфрама изготовляют из очищенной неотожженной молибденовой проволоки, относительное удлинение которой не должно превышать 3%. Также предъявляются требования к прочности молибденовой проволоки, ее поверхности, допускам по размерам. Так, проволока должна иметь гладкую поверхность, прочность при растяжении около 130 кг/мм2, овальность не более 2%, допуски по диаметру проволоки должны быть строго соблюдены. Вольфрамовая спираль навивается на керн из молибденовой проволоки, а затем вместе с керном подвергается отжигу. Условия отжига требуют применения в качестве материала керна тугоплавкого металла высокой чистоты, который обладает высокой прочностью при нагревании и может быть удален химическим путем. Таким металлом и является молибден.
Молибден в виде проволоки нашел активное применение в производстве приемо-усилительных ламп. Данный металл используется в качестве конструкционного материала. Из молибденовой проволоки изготавливают сетки. Как правило, такие сетки несут высокую тепловую нагрузку и к ним предъявляются высокие требования по точности навивки. Молибден, в свою очередь, обладает высокой точкой плавления, достаточно формоустойчив при высоких температурах и имеет ряд других положительных свойств, которые делают данный металл широко применяемым в производстве сеток приемо-усилительных ламп. Также стоит отметить хорошую свариваемость молибдена с никелем, из которого изготовляют траверсы сеток.
Молибденовая проволока, предназначенная для изготовления сеток, должна иметь чистую блестящую поверхность. Проволока может быть твердой или мягкой, относительное удлинение должно быть в интервале от 0 до 20%, овальность должна быть минимальной: отклонения от абсолютно круглого сечения не должны превышать 1,5%. Твердость и относительное удлинение исходной проволоки определяется в зависимости от способа производства сеток.
Проволока из молибдена также применяется и в производстве генераторных ламп. Из нее изготавливают сетки, различные держатели накаливаемых катодов, упругие элементы (например, натяжные пружины для крепления катодов).
В рентгеновских трубках из молибденовой проволоки выполнены вводы катодов, которые герметично впаяны в тугоплавкое боросиликатное стекло, являющееся материалом колбы рентгеновской трубки.
Из молибденовой проволоки изготавливают нагреватели высокотемпературных электрических печей. Молибденовые нагреватели используют при температурах до 2000 °С. Нагрев осуществляется в защитной атмосфере, так как при взаимодействии с кислородом молибден легко окисляется.
Стандарты
- ГОСТ 27266-87 «Проволока молибденовая для источников света. Технические условия».
- ГОСТ 18905-73 «Проволока молибденовая. Сортамент».
- ТУ 48-19-290-91 «Проволока молибденовая типа Спрабонд».
§3. Молибденовые листы (ленты, полосы, фольга, пластины)
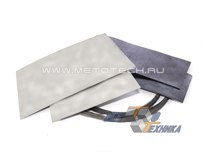
Как правило, плоский прокат из молибдена - лист, лента, полоса, пластина, фольга - получают применением двух операций - плоская ковка и прокатка. В качестве заготовки используются молибденовые штабики различных размеров.
Наиболее распространенными заготовками для получения молибденовых пластин толщиной 2-8 мм являются молибденовые штабики прямоугольного сечения с размерами 25х25 мм, 12,5х12,5 мм и 8х8 мм. Плоскую ковку таких штабиков, как правило, осуществляют пневматические молоты. Схематичное изображение молота представлено на рисунке.
Устройство пневматического молота
1 – молот, 2 – молибденовый штабик, 3 – наковальня
Перед ковкой заготовки подвергаются нагреву. Плоскую ковку по сравнению с круглой (см. Глава 3 §1) ведут при более высоких температурах. Так при плоской ковке температура нагрева составляет 1500-1600 °С в начале процесса и около 1000 °С в конце. Нагрев заготовок осуществляется с помощью муфельных печей, расположенных рядом с молотом. После нагрева штибики подаются под молот с помощью специального механического устройства. Ковку ведут до получения пластины определенной толщины, которая зависит от размеров исходного штабика. Толстые штабики обычно проковываются до толщины, равной 1/3 от исходной, более тонкие – до 1/4 исходной толщины. Например, молибденовый штабик сечением 25х25 мм куют до получения пластины (листа) толщиной 8-10мм, штабик сечением 12,5х12,5 мм – до пластины толщиной 4 мм, штабик сечением 8х8 мм – до пластины толщиной 2 мм. После плоской ковки перед прокаткой молибденовые листы (пластины) очищают от слоя окислов. Очищение производят химическим способом. Пластины из молибдена погружают в расплав 90% гидроокиси натрия и 10% азотистокислого натрия. Также в процессе ковки на молибденовой пластине могут появиться небольшие трещины. Данные дефекты убирают путем шлифования.
После плоской ковки полученные молибденовые пластины подвергаются прокатке. Прокатка осуществляется в две стадии: горячая прокатка и холодная прокатка. Прокатку ведут на двухвалковых прокатных станах. Горячую прокатку осуществляют при температуре 1200 °С в начале процесса, которая затем снижается до 800-900 °С. Толщина молибденовой ленты, получаемой после горячей прокатки, зависит от толщины исходной пластины. Если толщина пластины составляет 8 мм, то горячую прокатку ведут до получения ленты (полосы) толщиной 1-1,2 мм. Молибденовый лист (пластину) толщиной 4 мм прокатывают до толщины 0,6 мм, а лист толщиной 2 мм - до полосы (ленты) толщиной 0,35-0,4 мм. После горячей прокатке полученные молибденовые полосы (ленты) подвергают химической очистке. Для этого их погружают в расплавленную смесь гидроокиси натрия и азотистокислого натрия, или в амиачный раствор перекиси водорода, или в кислый раствор бихромата калия.
После очистки ленты из молибдена подвергают холодной прокатке, которая производится при комнатной температуре. В результате этого процесса получают изделие необходимого размера. Также в процессе холодной прокатки материал приобретает необходимую пластичность. Если во время прокатки ленты (полосы) излишне нагартовываются, то производят их промежуточный отжиг. Отжиг молибденовых лент осуществляют при температуре не более 850 °С. После завершения холодной прокатки ленты из молибдена снова подвергаются очистке. Способы очистки аналогичны тем, что применяются после горячей прокатки. В качестве окончательной обработки лент (полос) может осуществляться их полировка мелким порошком окиси алюминия.
Применение
Молибденовая лента и полоса может использоваться в электрических печах в качестве нагревателей. В электровакуумной промышленности такие печи применяются для отжига спиралей и проволоки при высоких температурах. При изготовлении нагревателя молибденовую ленту изгибают, придавая ей форму цилиндра или полуцилиндра. Концы нагревателя закрепляют в массивных зажимах из молибдена. Нагрев осуществляется в среде защитного газа.
Молибденовые пластины (листы) часто применяют в качестве конструкционного материала при производстве изделий в авиа- и ракетостроении. Из них изготовляют тепловые экраны, элементы обшивки ракет и самолетов, а также другие детали, материал которых должен иметь высокую жаропрочность (см. Глава 1 §3).
Пластины, ленты, полосы и тонкая фольга из молибдена используются для изготовления анодов генераторных ламп. Аноды больших размеров, как правило, делают составными. Отдельные пластины соединяются с помощью клепки или точечной сварки.
Стандарты
- ГОСТ 17431-72 «Материалы порошковые. Листы из сплава марки М-МП. Технические условия».
- ГОСТ 25442-82 «Полосы молибденовые отожженные для глубокой вытяжки. Технические условия».
- ТУ 11-90 (Яе0.021.055 ТУ) «Полосы молибденовые для электровакуумной промышленности».
- ТУ 48-19-272-83 «Полосы молибденовые неотожженные. Технические условия».
- ТУ 48-19-245-84 «Фольга молибденовая. Технические условия».
- ТУ 48-19-472-90 «Заготовки листовые мерные из молибдена марок МЧ и МЧВП».
- ТУ 48-19-315-89 «Полосы молибденовые для электровакуумной промышленности неотожженные. Технические условия».
- ТУ 48-19-273-91 «Прутки, поковки и листы из молибденового сплава марки ЦМ-2А. Технические условия».
§4. Молибденовый порошок
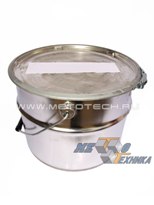
Молибденовый порошок получают из ангидрида молибдена (молибденовой кислоты MoO3) путем восстановления водородом. Условия процесса восстановления определяются в зависимости от конечного назначения получаемого порошка. Молибденовый порошок, предназначенный для дальнейшего изготовления проволоки, прутков, листов и прочей продукции, должен содержать 99,9% молибдена и иметь мелкозернистую структуру. Порошок из молибдена, который используется при производстве сталей, должен на 99,0-99,5% состоять из молибдена и может иметь более крупные зерна.
Чистота получаемого порошка молибдена во многом зависит от чистоты исходной окиси MoO3. Очень важно, чтобы окись молибдена содержала незначительное количество примесей. Величина зерен получаемого порошка зависит от условий восстановления и от величины зерен окиси молибдена. Как правило, молибденовый порошок получается тем крупнее, чем больше величина зерен исходной молибденовой кислоты. Температура, при которой осуществляется восстановление молибдена, и концентрация водяных паров также влияют на величину зерен. Средняя величина зерна молибденового порошка растет с повышением температуры восстановления. Подбирая соответствующие условия восстановления и ангидрид молибдена MoO3 можно получить порошок молибдена со средней величиной зерна от 0,5 до 10 мк и больше.
Восстановление осуществляют в две стадии:
MoO3 + H2 ↔ MoO2 + H2O,
MoO2 + 2H2 ↔ Mo + 2H2O.
Такой подход препятствует значительному увеличению зерна. После восстановления полученный молибденовый порошок просеивают через мелкое сито и помещают в плотно закрывающиеся сосуды. Влажный воздух вредно влияет на порошок молибдена – последний начинает активно окисляться.
Свойства
Порошок чистого молибдена марки МЧ характеризуется набором свойств, таких как насыпной объем, объем утряски, коэффициент окисления. В таблице приведен пример численных значений указанных свойств для порошка молибденового МЧ.
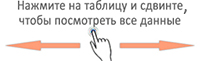
Вид порошка | Насыпной объем, см3/100 г | Объем утряски, см3/100 г | Коэффициент окисления | |
---|---|---|---|---|
измеренный | теоретический | |||
Чистый молибден | 70-110 | 45-62 | 48,4 | 50,03 |
Применение
Большая часть производимого молибденового порошка идет на изготовление сталей и чугунов. Молибден в данном случае выступает в качестве легирующей добавки, которая улучшает свойства получаемых сплавов (см. Глава 1 §3). При этом не предъявляются требования к высокой чистоте порошка молибдена. Молибденовый порошок может содержать до 0,5-1% примесей.
Другой областью применения порошка является производство компактного молибдена (см. Глава 2 §2). Компактный молибден в виде штабиков получают из молибденового порошка методами порошковой металлургии. Для указанных целей используют мелкозернистый порошок, содержание примесей в котором не превышает 0,1%. Из полученных штабиков компактного молибдена затем изготовляют прутки, проволоку, полосы, ленты, листы и другие изделия.
Стандарты
- ТУ 48-19-316-80 «Порошок молибденовый».
- ТУ 48-19-69-80 «Молибден металлический высокой чистоты».
- ТУ 14-22-160-2002 «Порошок молибденовый восстановленный».
Заключение
В данной статье рассмотрены различные аспекты, связанные с тугоплавким металлом молибден - свойства, области применения, производство, продукция.Как описано в статье, процесс получения данного металла состоит из многих стадий и является достаточно трудоемким. Авторы постарались выделить наиболее значимые этапы производства молибдена и обратить внимание на важные особенности.
Обзор свойств и областей применения молибдена показывает, что это очень важный материал, без которого в некоторых отраслях промышленности просто невозможно обойтись. Он обладает уникальными свойствами, которые в некоторых ситуациях нельзя получить путем применения других материалов.
Обзор выпускаемой промышленностью продукции из молибдена - проволоки, прутков, листов, порошка - позволяет лучше понять ее особенности, важные свойства и конкретные применения.
Авторы надеются, что приведенный в статье материал будет интересен и полезен читателям. Свои замечания и предложения читатели могут присылать на адрес info@metotech.ru.
Список литературы
- Агте К., Вацек И. «Вольфрам и молибден».
- Зеликман А.Н «Молибден».
- Елагин В.И., Колачев Б.А., Ливанов В.А. «Металловедение и термическая обработка цветных металлов и сплавов».
- Уткин Н.И. “Металлургия цветных металлов”.
- http://ru.wikipedia.org
- http://slovari.yandex.ru
- http://www.metotech.ru